The Complete Guide to Paper Roll Manufacturing: From Raw Materials to Finished Product
- Raghav jain
- Oct 9, 2024
- 4 min read
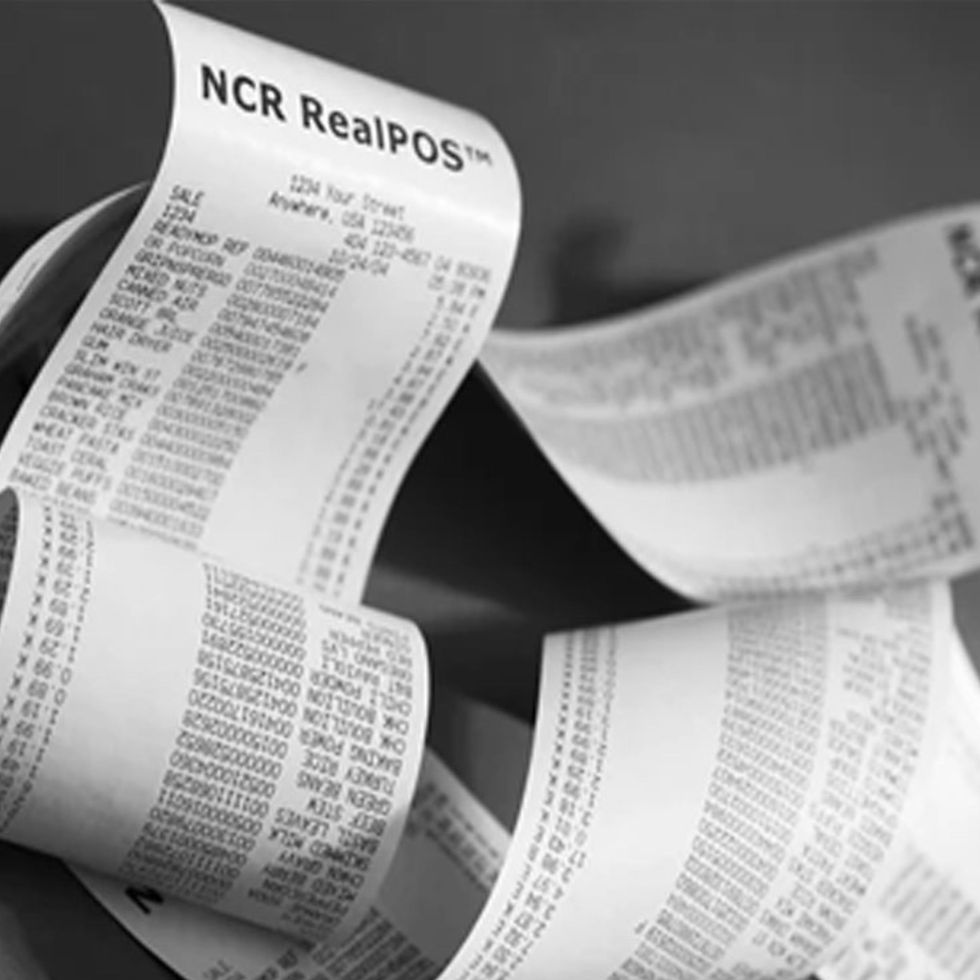
Paper roll manufacturing plays a crucial role in supplying a wide array of industries, from retail and logistics to banking and hospitality. As paper rolls are essential for printing receipts, labels, tickets, and more, understanding the entire production process is key to grasping their quality, availability, and sustainability. This comprehensive guide will take you through each stage of paper roll manufacturing, from sourcing raw materials to creating finished products, along with industry-specific insights and best practices.
Understanding the Basics: What Are Paper Rolls?
Paper rolls are continuous sheets of paper wound around a cylindrical core. They are used in a variety of applications, such as point-of-sale (POS) receipts, ATM receipts, fax machines, and labels. Paper rolls are made in different sizes and thicknesses, depending on their intended use. The most commonly known varieties are thermal paper rolls, bond paper rolls, and carbonless paper rolls.
Each type has its own unique characteristics and uses:
Thermal Paper Rolls: Ideal for receipt printers and POS systems, these rolls are coated with a heat-sensitive layer that darkens when exposed to heat, eliminating the need for ink or toner.
Bond Paper Rolls: Used in impact printers, bond paper rolls provide a smooth surface for printing with ribbons or inks.
Carbonless Paper Rolls: Commonly used for creating multi-part forms without the need for carbon paper.
Step 1: Sourcing Raw Materials
The first step in the paper roll manufacturing process is sourcing the raw materials. The primary raw material for most paper products is wood pulp, which is derived from softwood or hardwood trees. Depending on the type of paper roll being produced, other materials like recycled paper, clay, latex, and various chemicals are also added.
Wood Pulp: The primary raw material for paper production, wood pulp is made by breaking down the wood fibers through chemical or mechanical processes.
Additives and Coatings: For thermal paper, a special heat-sensitive coating is applied to the surface of the paper, while bond and carbonless papers may require additional chemicals to enhance print quality or durability.
Step 2: Pulping and Paper Production
Once the raw materials are sourced, they are processed to create pulp. This stage involves breaking down the wood chips into small fibers through a pulping process, which can be either mechanical (using mechanical energy to grind wood) or chemical (using chemicals to dissolve lignin).
Mechanical Pulping: This method uses mechanical grinding to break down the wood, producing a pulp with higher yield but less strength.
Chemical Pulping: Chemical pulping uses chemicals like sodium hydroxide and sodium sulfide to dissolve the lignin, resulting in a stronger pulp that is ideal for high-quality paper products.
After pulping, the fibers are washed, bleached, and screened to remove impurities. The pulp is then diluted with water and fed onto a paper machine, where it is formed into a continuous sheet of paper. The paper is pressed, dried, and then wound into large rolls, known as “parent rolls.”
Step 3: Converting Parent Rolls into Smaller Rolls
The large parent rolls are then moved to the converting stage. This is where the rolls are cut, slit, and rewound into smaller rolls that are more suitable for end-users.
Slitting: During the slitting process, the parent rolls are sliced into narrower widths using high-precision slitting machines. The width and diameter of the resulting rolls are determined by the specific requirements of the customer.
Rewinding: After slitting, the smaller rolls are rewound onto cores. This ensures that the paper is tightly wound and ready for use in various printing devices.
Core Insertion: Each roll is wound around a sturdy core, which provides stability and helps maintain the roll’s shape. The core size and material (cardboard or plastic) vary based on the application.
Step 4: Coating and Printing (Optional)
For thermal and carbonless paper rolls, additional coating and printing processes may be required:
Thermal Coating: A layer of thermal coating is applied to the paper surface, allowing it to react to heat during the printing process. This coating consists of dye and developers that produce sharp, clear images when exposed to a thermal print head.
Pre-Printing: Some paper rolls are pre-printed with logos, terms, and conditions, or security features like watermarks. This step is usually done for branding purposes or to enhance document security.
Step 5: Quality Control and Packaging
After the rolls are converted and coated (if applicable), they go through a rigorous quality control process to ensure they meet industry standards. Quality checks include:
Thickness and Width Measurement: Ensuring the rolls have uniform dimensions.
Surface Finish Testing: Checking for smoothness and the absence of defects.
Print Quality Verification: For thermal rolls, print quality is tested by applying heat to confirm the coating’s reactivity.
Once the rolls pass quality checks, they are packaged in boxes or pallets for distribution. Proper packaging prevents damage during transit and helps maintain the rolls' integrity.
Step 6: Distribution and Supply Chain Management
The final step in paper roll manufacturing is distribution. Manufacturers typically work with wholesalers, distributors, or directly with businesses to supply paper rolls in bulk quantities. Managing the supply chain effectively is crucial to ensuring timely deliveries and consistent supply for end-users.
Read also: Exploring the Common Applications of 3 1/8'' X 230' Thermal Paper Rolls Across Various Industries
Conclusion
The Paper Roll Manufacturing is a complex journey that involves multiple stages, from sourcing raw materials to converting parent rolls into finished products. Understanding each step helps businesses make informed decisions when choosing paper roll suppliers and evaluating product quality. With advancements in technology and a focus on sustainability, the paper roll industry continues to evolve, offering innovative solutions that cater to diverse business needs.
Comments